The U.S. aluminium industry is at a breaking point – and that’s not an overstatement. With new tariffs now extending to Canada under Section 232, the rules of the game have changed. What was once considered a “domestic” flow of aluminium from our northern neighbour has been reclassified. The result?
A 3-million-tonne gap in supply, and a scramble to fill a growing 5-million-tonne deficit between U.S. demand and domestic production.
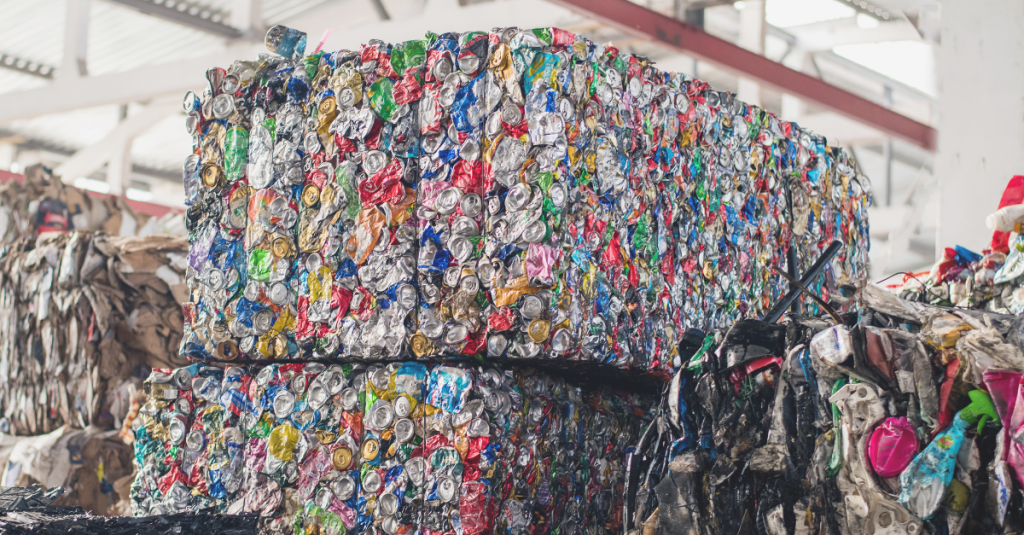
This isn’t just a trade policy issue – it’s a wake-up call. For decades, we’ve relied on external sources to keep our aluminium ecosystem alive. Now, we’re paying the price. And while the headlines about building new smelters sound promising, reality tells a different story.
Building a smelter in the U.S. today? That’s not a five-minute project. It’s a five-year-plus endeavour that requires enormous capital, time, permitting, and one element we simply don’t have enough of: Green power.
Without reliable, sustainable energy, these smelters remain ideas on paper rather than real answers on the ground.
So, what do we do?
The answer isn’t louder headlines – it’s smarter infrastructure. That’s where recycled aluminium and high-efficiency remelting solutions step in. Instead of waiting years for megaprojects to break ground, we can act now with nimble, modular, and efficient systems designed to recover and process aluminium within U.S. borders.
The recycling gap
Aluminium is one of the most recyclable materials on Earth. It can be melted and reused endlessly with only a fraction of the energy required to produce it from ore. Yet, in the United States, we fail to capitalise on this advantage.
The numbers speak for themselves: although recycling aluminium uses only 5% of the energy of primary production, we’re recovering far less than we could. A massive percentage of post-consumer scrap, especially used beverage cans, coated materials, and contaminated extrusion profiles, gets downcycled, landfilled, or exported. Why?
Because we lack the infrastructure to process it cleanly and profitably here at home.
It’s not a matter of technology. The solutions exist: advanced sorting systems, dryer units, decoating lines, regenerative melting furnaces, and automated material handling. These systems are already in operation across Europe and Asia, achieving impressive yields with minimal emissions. But in the U.S., adoption has been slow and fragmented.
From raw potential to real capacity
The time has come to see aluminium recycling not as a side industry, but as a national imperative.
We should be building compact, regional, high-efficiency melting centres powered by renewable energy. We should be equipping them with inline filtration, degassing, and launder systems that boost metal recovery and improve alloy quality. And we should be supporting this with policies that encourage closed-loop manufacturing and post-consumer scrap collection.
If we focused even a fraction of the investment currently going to primary production into building out secondary aluminium systems, we’d begin to close the gap faster and more sustainably.
Because here’s the truth: it’s easier, cheaper, and greener to produce aluminium from scrap than from ore. The bottleneck isn’t chemistry—it’s commitment.
Policy needs to catch up
While the Bipartisan Infrastructure Law and Inflation Reduction Act have created a wave of optimism, there’s still no unified aluminium strategy. Incentives target batteries and EVs, but overlook the base materials needed to make them work.
What we need is a dedicated plan to decarbonise aluminium, not just on the supply side, but across the entire life cycle. That includes recycling incentives, modernised permitting for melting facilities, support for clean energy connections, and tax credits for companies that choose low-carbon alloys.
The case for acting now
Every delay comes at a cost, not just in dollars, but in competitiveness.
As global markets tighten, countries that can secure domestic low-carbon aluminium will have a strategic advantage. They’ll be able to build EVs, solar panels, airplanes, and defence systems faster, cheaper, and with a lower carbon footprint.
Meanwhile, those who wait will find themselves squeezed, paying premium prices for imports or battling to catch up in an industry already moving forward.
Final Thought
If the U.S. is going to lead the next chapter of industrial growth – one that’s clean, smart, and resilient, then aluminium must be part of the foundation. But not the aluminium of the past! Not the smelters that take decades and megawatts to build. The aluminium of the future is local, circular, and efficient.
It’s time to stop seeing aluminium recycling as a backup plan and start treating it as the main plan.