In my last column, I wrote about a dilemma that most small and mid-sized aluminium extruders live with: the constant trade-off between cutting prices to stay competitive and protecting product quality to survive. I suggested there’s a third path, upgrading.
But before we talk about what that looks like, we need to understand what we’re up against.
In recent conversations with several extrusion plant owners, including those I met during the Aluminium China Expo in Shanghai, a clear picture emerged. Everyone agreed that scaling output while preserving quality sounds good in theory. But in practice, it’s a battle, one that wears you down at every stage of production unless the fundamentals are rock solid.
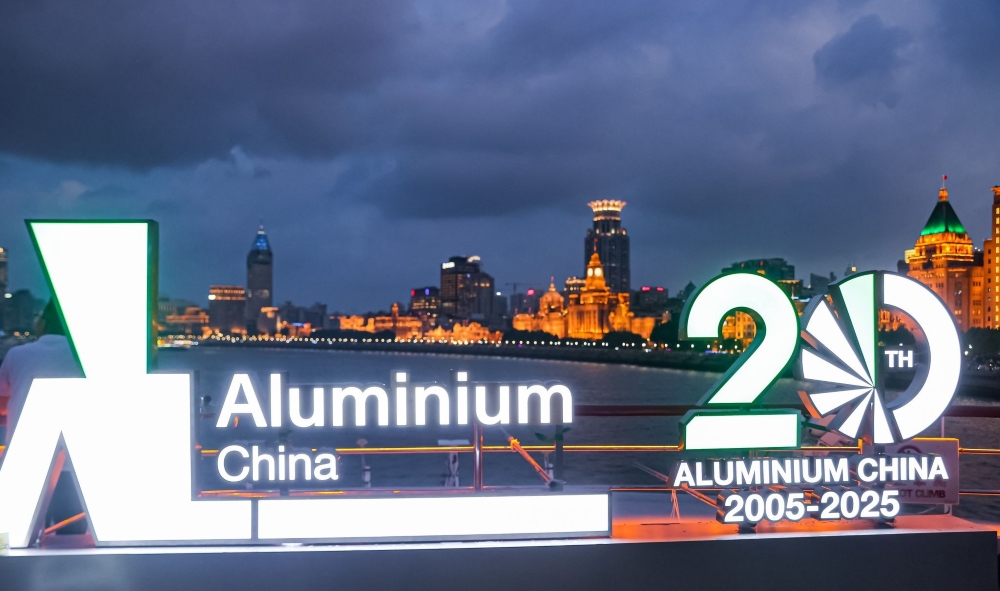
Image credit: ALUMINIUM CHINA
That led me to borrow a page from Elon Musk’s playbook, to look at the problem from first principles. Forget legacy methods or industry assumptions. What happens if we break down the extrusion process from the ground up and ask: where exactly does quality fail when volume increases?
Here’s what came out of that exercise:
The 11 silent quality traps in aluminium extrusion
- Feedstock: Quality starts before the melt
Low-grade scrap or outsourced billets bring hidden risks: alloy mismatches, contamination and zero traceability. A bad melt can’t lead to a good product.
- Melting without discipline
Lack of control in degassing, temperature and slag removal turns melting into guesswork, especially when production is rushed.
- In-house casting: Controlled chaos
Improper billet cooling and unchecked surface flaws often fly under the radar when volume is the priority.
- Homogenisation: Not just a time cycle
Shortened soak times or mixing batches in ageing ovens create inconsistent grain structures and mechanical performance issues.
- Dies: Small tools, big impact
Dirty or worn dies, reused under pressure, slowly destroy dimensional consistency. Scaling amplifies the damage.
- Pressing: Precision vs throughput
Small deviations, likely, ram speed, billet temperature and press alignment can multiply fast under tight cycle times.
- Cooling: Uniformity is everything
Using the same quench strategy for varied profiles or alloys causes distortion and inconsistency.
- Stretching: A subtle science
Go too far and profiles deform. Too little and internal stresses remain. Speed leads to error.
- Heat treatment: Quietly cut short
To meet tight dispatch targets, ageing cycles are quietly skipped or shortened, affecting long-term reliability.
- Surface handling: Scratches that stick
Handling errors, likely scratches, stains and dings can undo all the upstream effort in seconds.
- Packing: The final weak link
Improper wrapping, mixed bundles or moisture ingress during transport lead to product rejections and brand damage.
So, what does this really mean?
Quality doesn’t fail at one dramatic moment. It seeps away in small, unnoticed steps until rejection rates rise, deadlines slip and discounts become your only option.
When plants scale without control, the cracks start to show. And no amount of firefighting at the end can fix upstream discipline.
Getting quality at scale isn’t about buying the most expensive machine. It’s about system thinking, repeatability, real-time feedback and a culture that doesn’t accept “good enough” when volume increases.
What’s next?
In the next column, I’ll share upgrade strategies that extrusion plants can adopt, starting with better melting practices, smarter die management and affordable in-line quality feedback to protect quality without inflating cost.
Because the real path forward doesn’t start with shortcuts. It begins with smart moves in the right place, at the right time.