Introduction
When we think of modern aviation and space exploration, we often picture powerful jets soaring through the skies or rockets launching into orbit. But behind these remarkable feats lies a silent hero – aluminium. Its exceptional properties have made it the backbone of aerospace engineering, enabling lighter, stronger and more fuel-efficient designs that have transformed aviation and space industries.
The history of aluminium in aerospace
The early days of aviation saw wooden aircraft dominate, but World War I marked the transition to aluminium. In 1915, German designer Hugo Junkers built the first all-metal aircraft, the Junkers J 1, using an aluminium alloy. The 1920s, known as the Golden Age of Aviation, saw racing and commercial aircraft innovations, leading to all-metal designs like the Ford 4-AT “Tin Goose.” By the 1930s, aluminium-based stressed-skin construction became the norm. During World War II, aluminium production soared to meet military demands, with the U.S. producing over 296,000 aircraft, solidifying aluminium’s role in aerospace.

Source: WW1 Aviation Heritage Trust
Key innovations in aluminium for aerospace
Over the decades, aluminium has evolved through advanced alloying to meet the demanding conditions of aerospace. Alloys such as 2024, used in aircraft skins, cowls and structures and 7075 is known for its high strength and structural reinforcement, plays a vital role in aircraft manufacturing, repair and restoration. In recent years, aluminium-lithium (Al-Li) alloys offer up to 10 per cent weight savings leading to up to 20 per cent better fuel efficiency, at a lower cost than titanium or composites. Aluminium has also been vital in spacecraft construction from satellites to rocket components and even modules on the International Space Station, due to its durability, malleability and heat resistance.
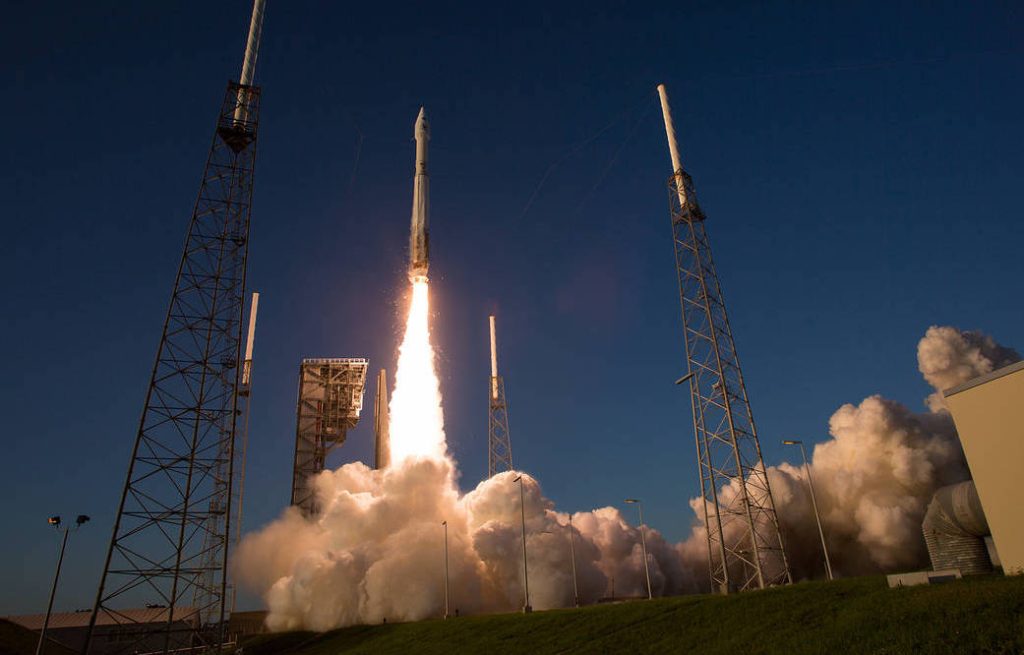
Source: Light Metal Age Magazine
Innovations like friction stir welding and 3D-printed aluminium parts are further expanding the potential of this metal, allowing for complex structures and improved manufacturing efficiency in aerospace applications.
Benefits of using aluminium in aerospace applications
With its lightweight nature and high strength-to-weight ratio, aluminium remains the preferred metal for aerospace applications. It offers several key advantages, including:
- Durability in high-stress environments, withstanding extreme temperatures and pressure.
- Formability, allowing easy fabrication of smaller aircraft components.
- High electrical conductivity, making it ideal for aviation systems.
- Cost-effectiveness, as its light weight reduces fuel consumption, leading to significant savings.
Aluminium sheets, plates and bars are widely used for aircraft structures, while tube, pipe and specialised shapes provide additional options for aerospace applications.
Future outlook
Aerospace Aluminium Market was valued at USD 7,638.86 million in 2023 and is expected to grow from USD 8,696.50 million in 2024 to USD 15,152.77 million by 2032, reflecting a compound annual growth rate (CAGR) of 7.2% during the forecast period (2024–2032).
Factors driving the future of aluminium in aerospace are advancements in composites, 3D printing and smart technologies. Aluminium-carbon fibre hybrids enhance strength while maintaining low weight, revolutionising aircraft design. Additive manufacturing enables complex, lightweight structures with minimal waste. Smart technologies, including embedded sensors and IoT, improve structural health monitoring, predictive maintenance and adaptive morphing structures for fuel efficiency. AI-driven manufacturing optimises production while self-healing coatings enhance durability. Aluminium’s integration with autonomous systems and space applications ensures its continued dominance in aerospace. With ongoing innovations, aluminium remains at the forefront of efficiency, performance and sustainability in aviation and space exploration.
Conclusion
From its early use in aviation to its cutting-edge applications in space, aluminium has been a cornerstone of aerospace innovation. Its combination of strength, lightweight and sustainability ensures it will continue to drive high-flying efficiency for decades to come.