In today’s world, the defence industry requires higher strength and readiness, playing a critical role in maintaining peace and security. It is no surprise that aluminium is a metal that is extensively used in diverse sectors and industries including the defence industry.? This is especially true when it comes to maintaining security and peace with higher strength and agility.
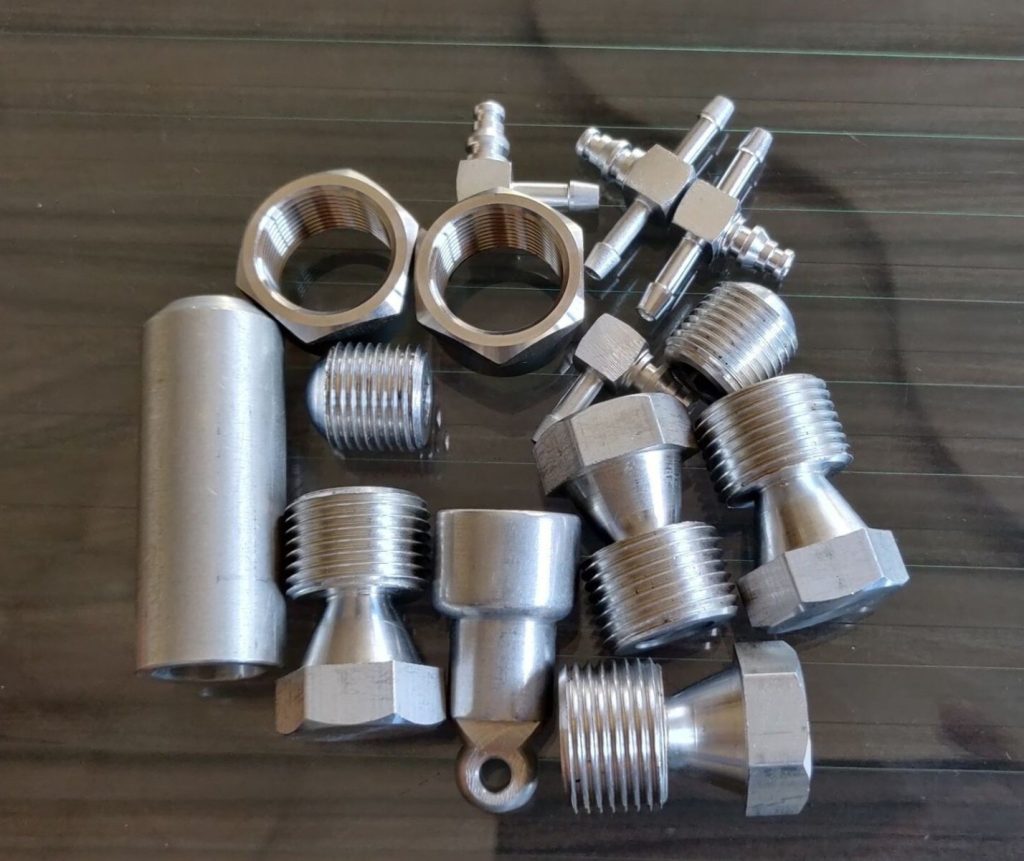
Image source: IndiaMART
In 2023, the defence industry used a total of 1.29 million tonnes of aluminium extrusions. Moreover, it is forecasted that the aluminium usage CAGR is expected to grow to 3.1 per cent by 2030 only within the global defence industry. This blog will cover how and where aluminium extrusion is used in the defence industry. We shall further assess aluminium extrusion in the defence industry depending on its properties like strength, efficiency and innovation.
Aluminium: an essential metal for modern defence applications
Aluminium is considered to be an ideal choice for global defence industry applications because of its high strength-to-weight ratio, fracture toughness, corrosion resistance, excellent fatigue strength and good workability. Different aluminium alloys are being used in defence applications in various forms of sheets, extrusions and forgings. High-strength aluminium alloys can be seen applied to military aircraft & helicopters, missiles, rockets and so on. In the case of truss structures of the International Space Station, the heavy use of extruded aluminium is done.
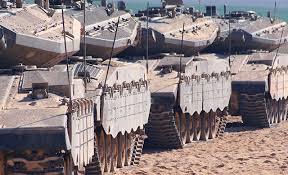
Image source: Harrison Casting
Applying aluminium across the defence sector
With unmatched strength, exceptional corrosion resistance and lightweight attributes, aluminium extrusion in today’s time has been an essential application. Why? Because they have been providing bolstering performance, higher reliability and serve as indispensable components. Let’s see how aluminium extrusion is applied in different critical areas of the global defence industry:
Aircraft & aerospace applications
Notably, the Wright Flyer, used in the Wright Brothers’ first powered flight in December 1903, featured a cast aluminium engine block to reduce weight. Today, advanced aluminium-lithium alloys for extrusions and forgings provide aircraft manufacturers with significant weight and fuel savings compared to the latest composites.
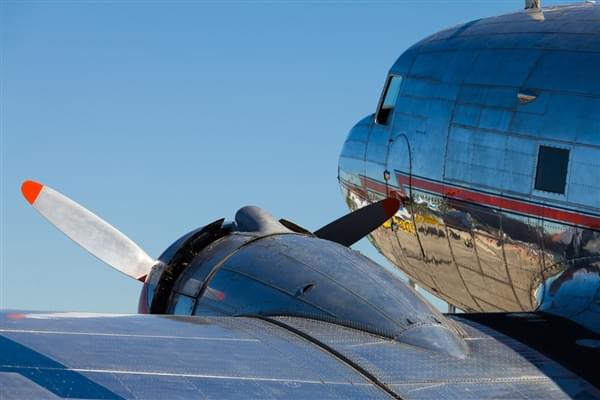
Image source: profall
They are extensively used in the fuselage and frame structures, ensuring high-stress resistance while reducing weight. In aircraft wings, control surfaces and landing gear assemblies, extruded aluminium enhances aerodynamics, supports structural integrity and withstands repeated stress cycles. Fuel and hydraulic systems rely on aluminium tubing for corrosion resistance and efficient fluid transport.
Navy applications
Aluminium profiles are widely used in naval applications, including ship and submarine construction. Designed for the demanding marine environment, these profiles offer high structural strength while remaining lightweight and resistant to corrosion from seawater and salt air.
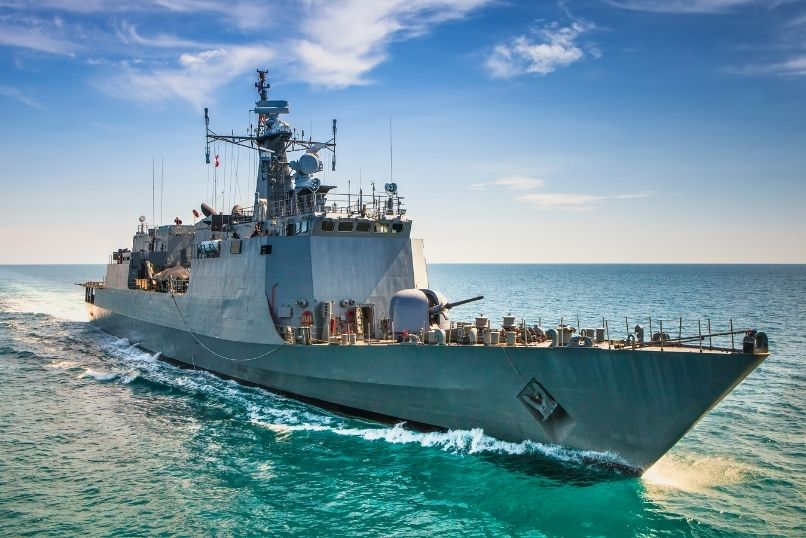
Image source: Wieland Diversified Metals
Weapon system applications
Aluminium profiles are essential in weapons systems, including missile launchers and gun mounts. Their strength and lightweight nature enhance accuracy and reliability in combat, improving the effectiveness of military operations.
*For more insights into other applications of aluminium extrusion in defence, read The World of ALuminium Extrusion- Industry Forecast 2030
Aluminium extrusion in defence enhances strength, efficiency and innovation.
Aluminium extrusion plays a crucial role in the defence sector by offering an optimal balance of strength, efficiency and innovation. Its high strength-to-weight ratio makes it ideal for military vehicles, aircraft, naval vessels and weapons systems, ensuring durability without compromising mobility.
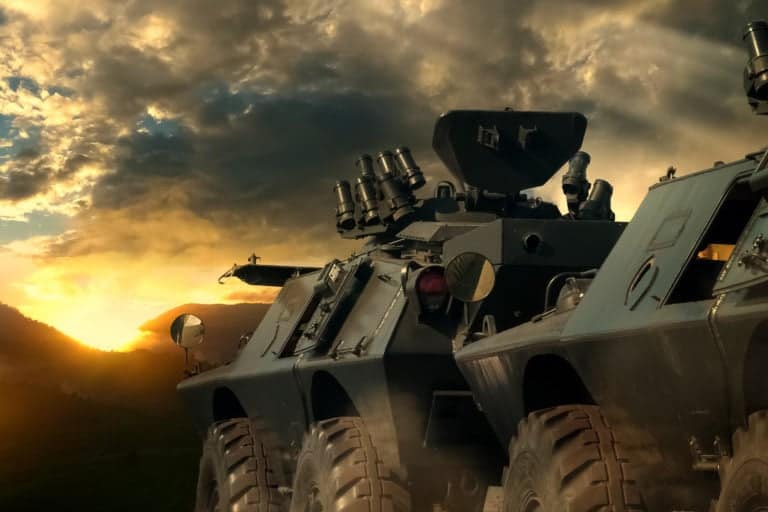
Image source: G. E. Mathis Company
Aluminium’s corrosion resistance allows it to withstand harsh environments, from marine operations to aerospace missions, reducing maintenance needs and extending the lifespan of critical defence equipment. The efficiency of aluminium extrusion lies in its ability to create complex, customisable shapes that enhance structural integrity while minimising material waste. This process supports lightweight designs that improve fuel efficiency and operational performance.
Innovation in aluminium alloys and advanced extrusion techniques continues to drive improvements in defence applications, enabling the development of stronger, lighter, and more resilient components. As military technology evolves, aluminium extrusion remains key in enhancing defence capabilities and ensuring mission success across land, sea, and air.
Conclusion
Aluminium extrusion is an indispensable asset in the defence sector, providing unmatched strength, efficiency and innovation. Its lightweight nature and durability make it ideal for military aircraft, naval vessels and advanced weaponry, ensuring superior performance in demanding environments. The material’s corrosion resistance and ability to withstand high stress enhance operational longevity while reducing maintenance.
As the defence industry evolves, advancements in aluminium alloys and extrusion techniques will further improve structural integrity, fuel efficiency, and combat readiness. With growing applications across land, sea and air, aluminium extrusion remains a cornerstone of modern defence technology, driving future advancements and security.