Every year marks a celebration of technological progress in the aluminium industry, and 2024 is no exception. After all, technology now plays the most crucial role in revolutionising the aluminium industry, helping it keep pace with advancements across the worldwide industrial manufacturing sectors. This year, many groundbreaking digital solutions and state-of-the-art tools have empowered the aluminium industry to achieve a new edge in operations by tracking carbon emissions, controlling downtime, improving energy efficiency, and reducing operational costs.
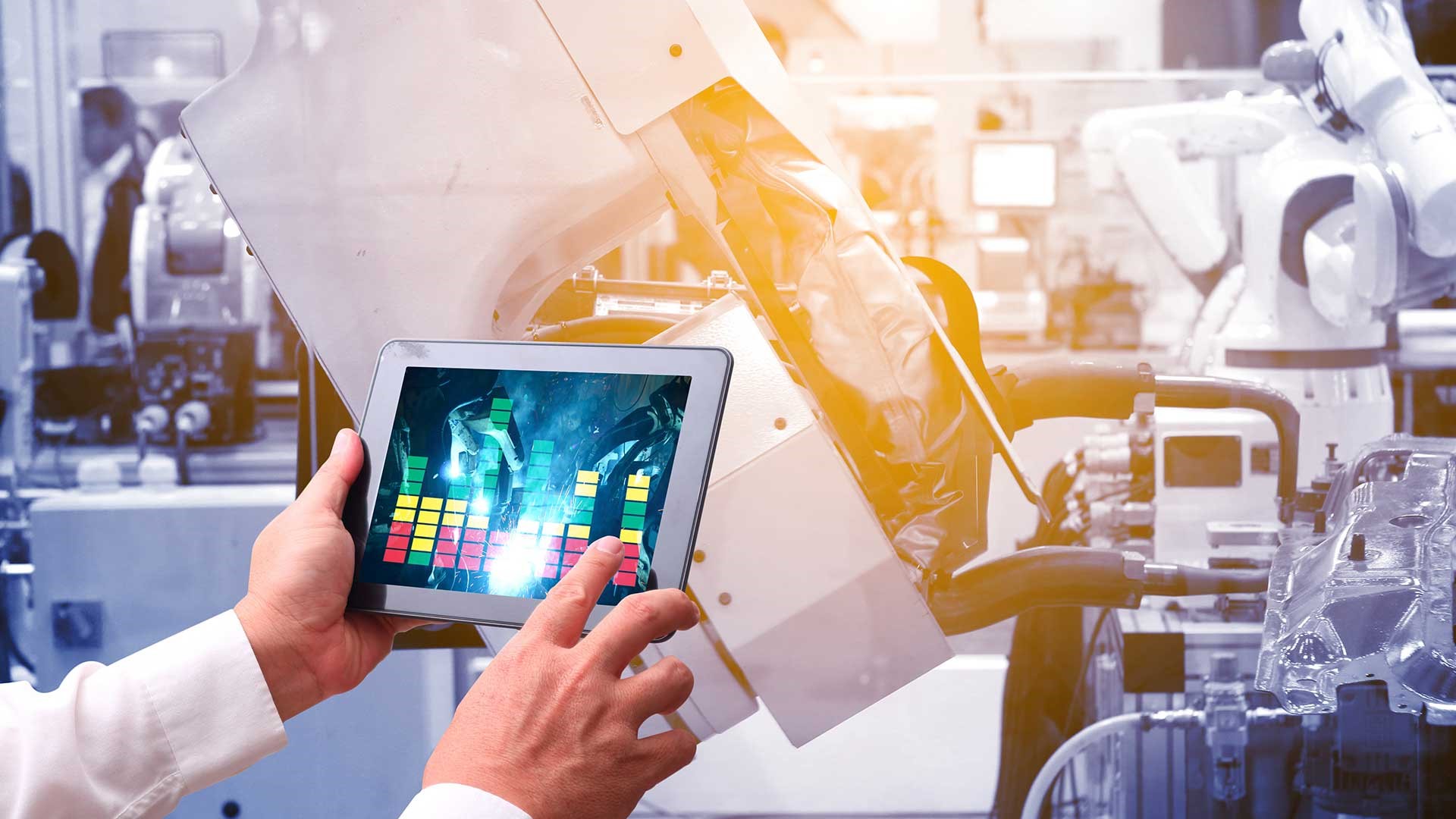
Alumtek Minerals’ (AM) latest technology to extract critical minerals from bauxite residue tops the list. The company has developed a unique technology that advances commercialisation efforts to extract rare earth elements and metals from bauxite residue, generating dual revenue streams. The technology also tackles the environmental and community hazards posed by red mud, an alkaline by-product of the alumina industry typically stored in tailing dams. This innovative approach facilitates the extraction of critical minerals like vanadium, titanium, gallium, aluminium hydroxide (essential for primary aluminium production), and high-purity iron oxide.
EGA advanced its exclusive smelting technology, DX+ Ultra, to the next generation with more futuristic features. The upgraded version is called EX, which had its design completion in July. A more advanced iteration of the DX+ Ultra, the EX-reduction cells are designed to boost smelter capabilities with increased amperage, increase production capacity by up to 22 per cent, and improve current efficiency. The technology comes in two variants: one prioritising productivity and the other aiming to minimise greenhouse gas emissions. In December, EGA broke ground to start constructing ten pilot reduction cells for the EX, expecting the first batch of production from the pilot reduction cells by the first half of 2025.
The German automotive and arms manufacturer Rheinmetall’s thriving thermal management division is expanding further, marking a significant milestone by introducing an inventive plug-and-play heat pump solution to be integrated into a hydrogen-powered truck for the first time. The thermal module, already prevalent in battery-powered commercial vehicles, construction equipment, and marine vessels, has achieved a significant breakthrough. Rheinmetall has successfully advanced the integration of this innovative plug-and-play solution into a cutting-edge fuel cell-powered truck, marking a milestone in its adoption within a forward-looking sector.
Three students from the National University of Science and Technology (NU), Oman—Al Yaqeen Amur Asuti, Reem Ahmed al Qassabi, and Ahamed al Awad—have developed an innovative device that converts palm waste into circular green aluminium. Their project, titled ‘Green Initiative for Utilising Omani Palm Waste to Produce Circular Green Aluminium’, marks a groundbreaking step toward fostering a zero-waste, sustainable economy in Oman. The device extracts lignin, a complex organic polymer, from palm waste and mixes it with commercial aluminium to create a more sustainable, recyclable, and environmentally friendly material. This zero-waste technology represents a significant step forward in Oman’s resource innovation.
A team of scientists led by Professors RB Harikrishna, Hemagni Deka, T Sundararajan, and G Ranga Rao from the Department of Chemical Engineering at IIT Madras has successfully demonstrated the utilisation of discarded metal wastes like aluminium cans as feed materials for the thermochemical production of green hydrogen. In this process, hydrogen gas is generated by splitting water using industrial waste metal scrap at elevated temperatures. The scientists specifically investigated the reaction between aluminium scrap and steam for hydrogen production. Their method achieved a production rate of 500 mL of green H2 per gram of scrap material at 1150°C, with an impressive conversion efficiency of approximately 94 per cent. To know more about the innovation, click here.