While we always consider aluminium as the metal for crucial applications in automotive, aerospace, energy storage and building and construction for its unique properties like high strength-to-weight ratio, corrosion resistance, superior electrical conductivity and so on. But, the process of deriving aluminium and alumina from its ore bauxite offers challenges in which opportunities are in disguise.
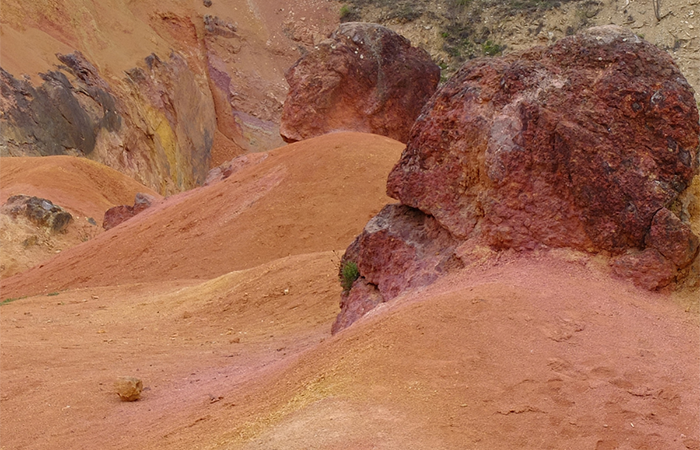
Critical Minerals are critical because of their rare and complex occurrence. Global demand for critical minerals is increasing day by day because of increasing dependence on alternative source of energy and storage of the same. Also, digital economy and its importance for industrialisation with reduced wastage, valorisation of waste are creating demands for certain critical minerals world wide.
India’s identified list of 23 critical minerals are going to play crucial role for country’s decarbonisation programs and digital economy. But the question is how all these are connected to Primary Aluminium Industry which is as large as 70 million tonnes worldwide.
In carbon emission reductions alone, the World Bank estimates that about 3 billion tonnes of critical minerals will be needed to decarbonise the global energy system by 2050. The production of minerals such as graphite, lithium and cobalt needed to increase by nearly 500% by 2050 to meet the need for clean energy.
Quite interesting, few of these critical minerals are actually possible to be sourced from Alumina Refinery. My focus for discussion is on this today.
Gallium which forms very critical semiconductor with Arsenic like Gallium-Arsenide actually occurs in Bauxite though in ppm (Parts Per Million). Alkali Digestion renders this mineral in soluble form in refinery and it is possible with alteration of process and process equipment to recover this critical mineral.
Red mud (bauxite residue) is a waste by-product generated from the refinery during the processing of bauxite ore. A typical bauxite plant produces 1–2 times as much red mud as alumina. This ratio is dependent on the type of bauxite used in the refining process and the extraction conditions. It is logical to consider that all Primary Aluminium producers will look forward to valorising the huge inventory of 3 billion tons to disrupt the economic state of the same.
Rare earth elements (REEs) do not generally occur in concentrated conditions in any ores so there is limited primary production of REEs. On the supply side, REEs are distributed in the earth’s crust in a sporadic manner as they lack chemical affinity to combine with ore-forming anions. REEs are therefore being produced as a by-product of other metal production. The most abundant REE in the earth is cerium (approximately 50 mg/kg), followed by neodymium and lanthanum, with heavier REEs being less abundant, and thulium being the least (<0.5 mg/kg).
Scandium is the most strategic one with crucial applications. There has been no primary source of scandium deposits with concentrations over 100 ppm. Hence, secondary resources such as red mud with a scandium content between 50 to 80 ppm can be considered important ore. Scandium’s strategic applications revolve around its use in high-tech alloys, solid oxide fuel cells (SOFCs) and specialised lighting, primarily in the aerospace, automotive and energy sectors. Its ability to enhance the strength and durability of Aluminium alloys, as well as its role in improving SOFC efficiency, makes it a valuable material for various industries, including aerospace, transportation and energy production.
Recovery of such precious rare earths from Red Mud is a big challenge in terms of processing and cost of the same. This will also ask for deployment of Scientific and Engineering man powers, suitable Capital Expenses. It is a challenge yet an imperative that such secondary sources be considered and a Road Map for a holistic utilisation of the Bauxite Residue with deep strategic perspective be initiated immediately.
A matured and cost-effective technology with innovative features will emerge maybe 3 to 5 years from now. It’s time for a Collaborative Business Model to back the innovation in terms of process and engineering, with participating user industries prepared by Primary Aluminium Producers. It is time Pilot-level activities are initiated with a huge amount of Scientific data already gathered from different investigations. The more time is taken to decide on a set of appropriate activities more the opportunity slips away to be ahead in this innovative and strategic initiative.