Aluminium dross – often viewed as an unwanted by-product of the aluminium industry – is undergoing a significant transformation. What was once dumped into landfills as hazardous waste is now increasingly seen as a resource to be recovered, recycled, and reintegrated into the value chain. As aluminium production and consumption continue to surge worldwide, so does the urgency to sustainably manage the dross it generates.
It is now believed that aluminium dross processing is no longer a side conversation in the aluminium sustainability narrative – it is essential to achieving a circular economy for the metal. This post provides our analytical take on the current state, emerging trends, and technological leaps redefining aluminium dross processing globally.
The scale of the challenge and opportunity
The aluminium industry is on a growth trajectory, with global consumption rising from 82 million tonnes in 2016 to over 100 million tonnes in 2024. As a result, the aluminium dross generation has also reached higher levels than in previous years, with Asia Pacific (including China) leading the market.
Yet, around 30% of this dross still ends up in landfills, causing environmental harm and economic loss due to unrecovered aluminium content. This is despite advances in dross processing technologies that today enable aluminium recovery rates upwards of 95%.
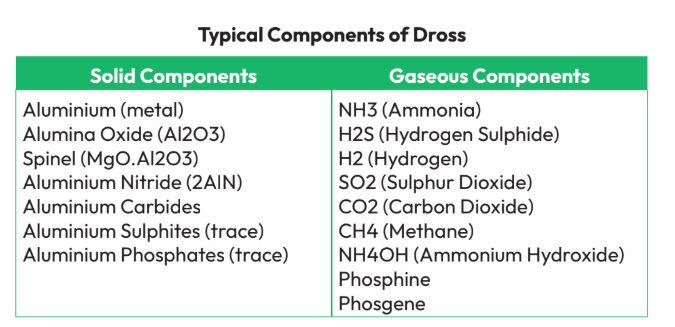
Source: Industry Sources
White vs Black Dross: Know the difference
Understanding aluminium dross starts with its classification:
White dross: Formed primarily in primary aluminium smelters, with high aluminium content (40–80%). It appears as lumpy material and holds significant potential for recovery.
Black dross: Generated in secondary aluminium and recycling units, containing lower metal content (5–25%) and higher oxide and salt content. It is granular in texture and poses higher environmental challenges.
Both types, if not managed properly, pose risks to the environment due to the release of flammable gases and the leaching of harmful salts. Yet, both also represent opportunities to recover aluminium, extract value-added materials, and contribute to zero-waste manufacturing.
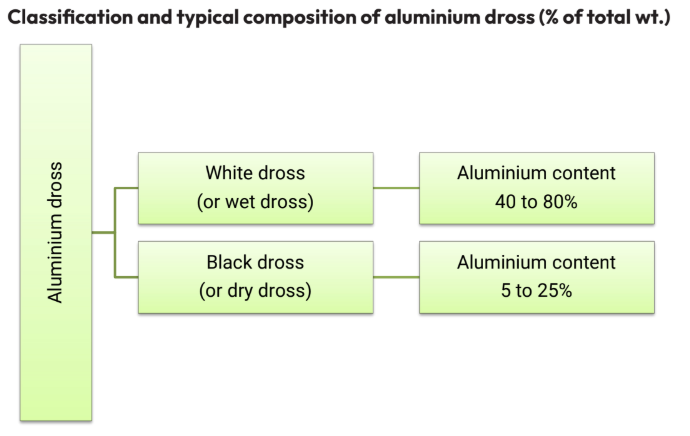
On-site vs Off-site processing: Two routes, different realities
Dross recovery generally follows two models:
- On-site (Hot) processing:
- Dross is immediately processed while still hot.
- Yields higher aluminium recovery with lower energy input.
- Requires capital investment in rotary salt or tilting rotary furnaces.
- Reduces transport-related emissions and costs.
2. Off-site (Cold) Processing:
- Dross is cooled, transported to third-party units, and then processed.
- Suitable for smaller operations without in-house facilities.
- Faces challenges like safe transport, oxidation losses, and salt slag disposal.
We see a growing preference for on-site solutions, which enable hot, salt-free dross processing with zero waste.
Technology is the game-changer
The dross processing sector has moved far beyond rudimentary mechanical separation. Modern technologies are tackling the dual challenge of maximising aluminium recovery and minimising environmental harm.
Some groundbreaking innovations include:
- TAHA’s salt-free and energy-efficient process recovers 90%+ aluminium and repurposes oxides for fertiliser and ceramics.
- ALTEK’s AluSalt™ system processes salt slag and recovers salts, alumina, and other by-products for reuse.
- Hydrova’s DrossZero not only recovers aluminium and salts but also generates green hydrogen, adding a clean energy dimension.
These proprietary technologies are proof that dross processing is evolving from a cost centre to a value creator.
Regional trends: The global perspective
Dross processing is not a uniform story globally. Here’s our regional snapshot:
- China dominates the dross generation with the maximum of global share.
- Europe and North America lead in terms of advanced recovery technologies due to stricter environmental regulations.
- Middle East & Africa, and South America show potential for technological catch-up, especially with increasing aluminium smelting capacity.
- Asia-Pacific (ex-China), including countries like India and Australia, are gradually shifting to sustainable dross recovery driven by industrial reforms.
Each region’s stage of aluminium industrial maturity dictates its approach to dross – from technology adoption to regulatory mandates.
Salt Slag: The next frontier
Beyond aluminium, salt slag – the hazardous residue from rotary furnace operations – is receiving due attention. Traditionally landfilled, it’s now being processed to recover:
- Aluminium (5–7%)
- Alumina (15–30%)
- Salts (up to 55%)
In recent years, several companies have developed salt slag recovery technologies to turn hazardous waste into safe industrial inputs. These technologies help reduce both environmental footprints and operational costs.
Dross to value: Industrial and environmental applications
- Processed aluminium dross isn’t just about metal recovery. It can be repurposed into:
- Construction materials (additive in cement and concrete)
- Steelmaking flux and deoxidisers
- Refractory materials
- Filler in asphalt and ceramics
- Even electrode material in energy storage devices like lithium-ion batteries
Innovative projects like the EU-funded SisAl Pilot are even exploring aluminium dross as a reductant in silicon production, showing potential for multi-sector circularity.
Dross processing is the unsung ‘Hero of Aluminium Circularity’
We firmly believe that aluminium dross processing should be viewed as a core sustainability pillar in the aluminium value chain. The case for deeper investment is clear, with nearly enough aluminium recovered from dross generated globally in 2024.
However, challenges remain:
- Underutilised capacity in downstream sectors.
- Lack of standardisation in small-scale processing.
- Environmental risks from untreated salt slag.
- Limited awareness among policymakers about its circular economy potential.
The aluminium industry needs policy support, tech scaling, and public-private partnerships to make dross recovery more mainstream and universally profitable.
Conclusion: Closing the loop is not optional – It’s inevitable
As global sustainability goals tighten and aluminium becomes even more crucial in clean energy, mobility, and infrastructure, dross processing is emerging as a strategic enabler of low-carbon growth.
We will continue tracking, analysing and supporting developments in this critical space because when waste turns into value, it’s not just good business—it’s smart industry.
Gain comprehensive insights into global aluminium dross generation, processing, and metal recovery. Discover detailed regional analyses of white dross and black dross/aluminium ash, along with insights across the primary production, downstream, and recycling segments.
Subscribe now to “Aluminium Dross Processing: A Global Review” for in-depth intelligence and strategic market perspectives.