A very Happy Republic Day to everyone! Team AL Circle takes immense pride in celebrating the spirit of our great nation. Let’s honour the values of freedom, unity, and progress that our Republic stands for and continue striving towards a sustainable and innovative future. Together, let’s build a brighter and sustainable tomorrow. Jai Hind!
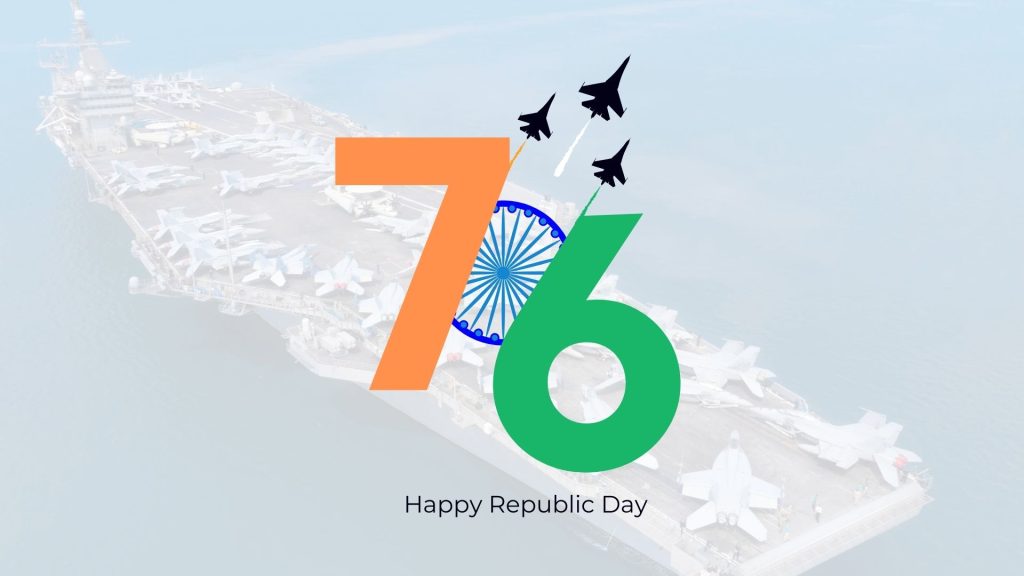
As the entire nation is laced up to celebrate the 76th Republic Day on January 26, 2025, this significant day not only marks the adoption of India’s Constitution but also commemorates the historic moment of “Purna Swaraj,” when India declared complete independence from British rule on January 26, 1930. ‘Swarnim Bharat – Virasat aur Vikas’ (Golden India: Heritage and Progress) is the theme for this year’s Republic Day military parade. And in this journey of progress and empowerment, aluminium has emerged as the material of choice for various defence applications—a role that dates back to 1892.
Since then, aluminium has been a trusted ally on the frontlines, contributing its strength, durability, and adaptability to an array of military equipment. As per the Defence Research and Development Organisation (DRDO), the country’s defence applications require about eight to ten thousand tonnes of wrought, speciality aluminium alloys per annum. This figure is growing steadily as more numbers of DRDO programmes attain production status (2018 DRDO data).
A brief history
The first notable application of aluminium in India’s defence sector was in the development of the BrahMos missile. The Defence Metallurgical Research Laboratory (DMRL) played a key role by creating indigenous aluminium alloys specifically designed for critical missile components. This milestone marked a significant step toward self-reliance in advanced aluminium alloy production for defence applications.
Across land, air, and water, India’s military relies heavily on aluminium. The transition to incorporating this advanced metal into defence equipment began in the post-1999 Kargil War era, a period marked by significant market changes and growing collaboration between the public and private sectors. This shift opened new avenues for aluminium, establishing it as a critical material for developing more efficient and durable defence technologies. It offers the dual advantages of lowering production costs while enhancing performance, all without compromising safety.
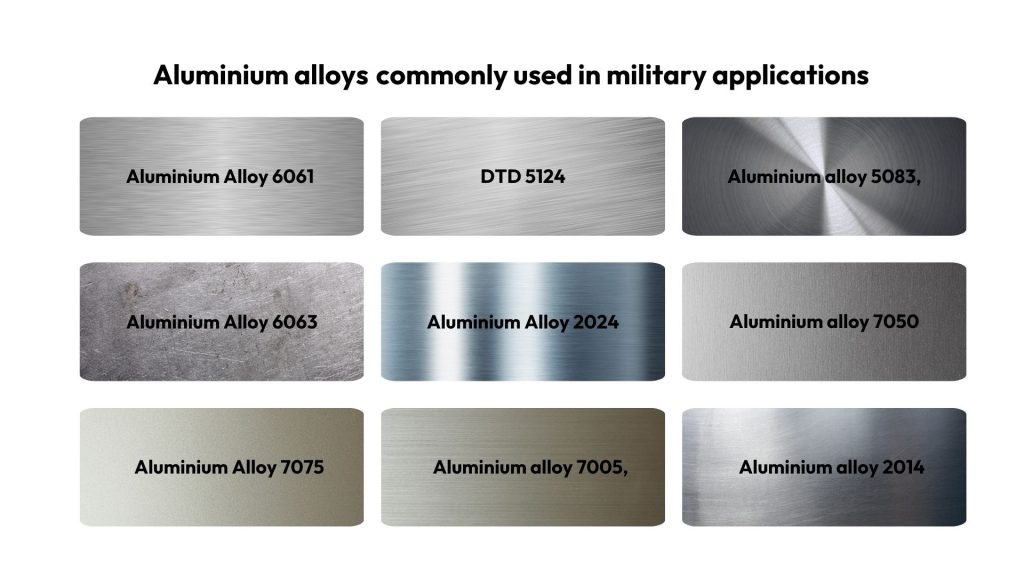
Defence Budget
In the Union Budget for FY 2024-25, the Ministry of Defence (MoD) has been allocated INR 6.22 lakh crore (approximately US $75 billion), the largest allocation among all ministries. This is an increase of about Rs 1 lakh crore (18.43 per cent) compared to the FY 2022-23 allocation and 4.79 per cent higher than the FY 2023-24 allocation.
While maintaining the allocation made to the Ministry of Defence (MoD) in the interim budget, the government has added an extra INR 400 crore for innovation in defence under the Acing Development of Innovative Technologies with iDEX (ADITI) scheme. Through this initiative, the MoD is collaborating with start-ups, MSMEs, and innovators to develop defence technology solutions and provide the Indian military with innovative, indigenous technologies. As per the current iDEX guidelines, a grant of up to 50 per cent of the product development budget, with a maximum limit of INR 25 crore per applicant, will be awarded.
Currently, the Indian defence sector is focused on fostering indigenisation in defence innovation, a cornerstone of its ‘Viksit Bharat’ vision. With the Prime Minister’s call for India to emerge as a global defence manufacturing hub, the country has set ambitious goals, targeting investments of INR 1.75 lakh crore in indigenous military production, including INR 35,000 crore earmarked for exports.
By 2025, India plans to double its domestic production and quadruple defence exports, which could significantly boost demand for domestically produced aluminium alloys. This push is likely to spur investments in production facilities and research, positioning aluminium as a key enabler of India’s defence ambitions.
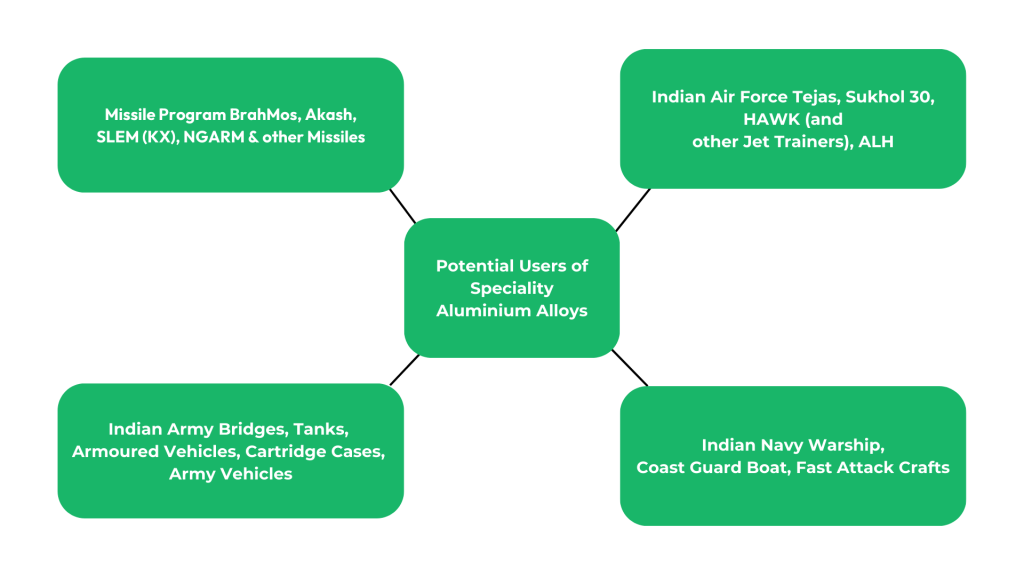
Use of aluminium in defence applications
- BrahMos
A supersonic cruise missile capable of being launched from multiple platforms is a collaborative project between Russia’s NPO Mashinostroyeniya (NPOM) and India’s DRDO. The missile achieves a maximum speed of Mach 2.8 (2.8 times the speed of sound), making the choice of aluminium alloys for its construction crucial. As per the information shared by DRDO, five different Russian grades of wrought aluminium alloys—1201, AK4-1Ч, AMГ6, AK6, and Д16Ч—are used across various missile components.
- Submarine Launched Ballistic Missile-K4
Aluminium alloy AA2219 plates with thicknesses of 30 mm and 20 mm, a width of 1400 mm, and lengths ranging from 4000 mm to 6000 mm were produced in annealed (O) and T87 tempers at BALCO, Korba. These plates were used to manufacture the nose cap dome, nose cap shell, and alignment cylinder components of the SLBM-K4 missile. DMRL provided all the required process parameters for producing these plates, ensuring the production of Class A1 ultrasonic quality plates for these critical applications.
- Akash Missile
Akash, a medium-range surface-to-air missile currently being produced for the Air Force and Army, features air intakes made from aluminium alloy AA6082 seamless tubes. These tubes are imported from various international sources in a straight form, with an outer diameter of 114 mm, a wall thickness of 2 mm, and a length of 1500 mm. The tubes are then bent to meet the design specifications and heat-treated to the peak-aged temper for their final application.
- New Generation Anti-Radiation Missile (NGARM)
Aluminium alloy AA6061 sheets with a thickness of 2.4 mm, heat-treated to annealed (O) and peak-aged (T6) tempers, were produced at BALCO, Korba for the fabrication of airframe components of the NGARM. DMRL provided essential metallurgical guidance, including process parameters and quality control procedures, to ensure the production of slabs and heat-treated alloy sheets with the required dimensions and mechanical properties.
- Naval Warship
Aluminium-magnesium-based alloys are extensively used in the manufacturing of naval warship superstructures. DMRL played a key role in providing essential metallurgical guidance to minimize the loss of magnesium during melting and casting, reduce hydrogen content in the molten metal before casting, and decrease rejections at various stages of the production process. This was achieved through precise control over rolling and heat treatment parameters for producing sheets and plates in various thicknesses (up to 30 mm) and desired tempers (H24 and M) at BALCO, Korba.
- Sarvatra Bridging System
7xxx series aluminium alloys are based on aluminium-zinc-magnesium and aluminium-zinc-magnesium-copper systems. The copper-bearing aluminium-zinc-magnesium system represents the highest strength class of aluminium alloys. These alloys can be made resistant to Stress Corrosion Cracking (SCC) through appropriate heat treatments. However, they are non-weldable.
- Fin Stabilised Armour Piercing Discarding Sabot (FSAPDS): An Anti-tank Ammunition
DTD5124 is an aluminium-zinc-magnesium-copper-based 7xxx series alloy, representing the highest-strength aluminium alloys produced through the ingot metallurgical route. The chemical composition of DTD5124 (introduced in the UK) closely resembles that of AA7075, an alloy produced by the Aluminum Company of America (ALCOA), USA.
- Futuristic Infantry Combat Vehicle (FICV)
Aluminium alloy AA2519 is used in the Advanced Amphibious Assault Vehicle (AAAV), an amphibious armoured personnel carrier. This alloy helps reduce the vehicle’s weight. However, there is no available information in the literature regarding the processing details of this material.
- HAL Tejas
The HAL Tejas is a single-engine, delta-wing, multirole combat aircraft developed by the Aeronautical Development Agency (ADA) and produced by Hindustan Aeronautics Limited (HAL) for the Indian Air Force (IAF) and Indian Navy. It made its inaugural flight in 2001 and was inducted into service with the IAF in 2015. Officially named “Tejas” in 2003, it is currently the smallest and lightest supersonic combat aircraft in its class. In addition to aluminium-lithium alloys and titanium alloys, carbon-fibre composite materials are prominently used in the construction of the Tejas. These composites make up 45 per cent of the airframe’s weight and 90 per cent of its surface area, the highest proportion among modern aircraft.
- Other ammunition
Aluminium-magnesium-silicon-based alloy AA6082 was produced as extruded rods in three different diameters—60 mm, 100 mm, and 150 mm—and heat-treated to T651 temper at OFAJ, Nagpur, under a DRDO project. This alloy offers an excellent combination of strength and corrosion resistance. It has been used in manufacturing rocket nozzles, mandrels for propellant casting, electronic housings, and various other components for different types of ammunition.
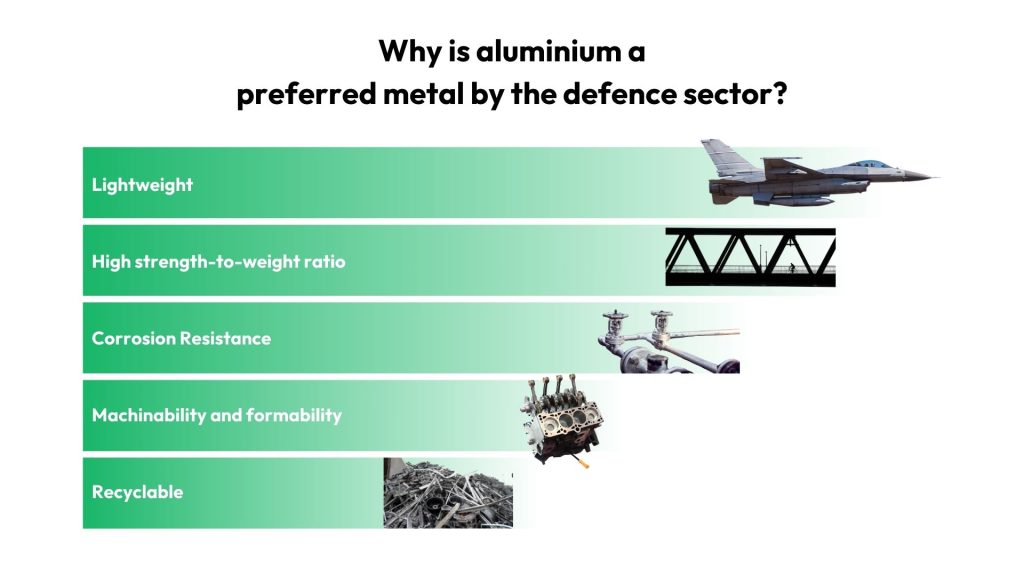
India- second-largest producer of aluminium
According to a 2024 press release from the Government of India, the country is the second-largest producer of aluminium, the third-largest producer of lime, and the fourth-largest producer of iron ore globally. The continued growth in iron ore and limestone production during the 2024-2025 financial year reflects strong demand from key industries like steel and cement.
This, along with the expansion of aluminium production, signals robust economic activity in the energy, infrastructure, construction, automotive, and machinery sectors. As aluminium is increasingly recognised as a critical and strategic metal, it is crucial for India to re-evaluate its policies. This isn’t just about enhancing economic competitiveness; it’s also about ensuring the country’s future in a world that increasingly values sustainability, resilience, and strategic independence.
According to AL Circle’s report, India’s current per capita aluminium consumption in 2023 was 3.1 kg and is likely to grow in response to the two-fold jump in demand by 2033 from 4.5 million tonnes at present to 9 million tonnes.
How has aluminium contributed in the development of India?
Aluminum has played a pivotal role in India’s growth by enhancing industrial output, generating employment, and contributing to GDP growth. Its versatility, lightweight nature, and recyclability have made it indispensable across sectors such as construction, medical science, green transition, and transportation. As a vital component in infrastructure development, aluminium supports India’s “Make in India” initiative, driving progress and innovation.
From smart vehicles to renewable energy infrastructure, aluminium’s applications extend across diverse industries, playing a crucial part in driving India’s transition to a developed, low-carbon economy. The flagship railway project, Vande Bharat, stands as a symbol of aluminium’s vital role in shaping a forward-looking national ecosystem aligned with the vision of Viksit Bharat by 2047.
Given the highly regulated pharmaceutical industry, aluminium foil packaging must adhere to strict standards and regulations established by health authorities such as the U.S. Food and Drug Administration (FDA) and the European Medicines Agency (EMA). These guidelines ensure that the packaging effectively preserves the quality and safety of medicines throughout their shelf life.
Use of aluminium in medical science
India’s healthcare sector has emerged as one of the country’s largest industries, contributing significantly to its economic growth through revenue generation and job creation. Key drivers include a growing middle class, rising demand for healthcare services, the expansion of medical tourism, and a robust pharmaceutical industry. These factors have stimulated the economy and created employment opportunities across various segments, such as hospitals, medical devices, health insurance, and clinical trials. Additionally, government initiatives like Ayushman Bharat have enhanced healthcare accessibility for a broader population, further fuelling economic progress.
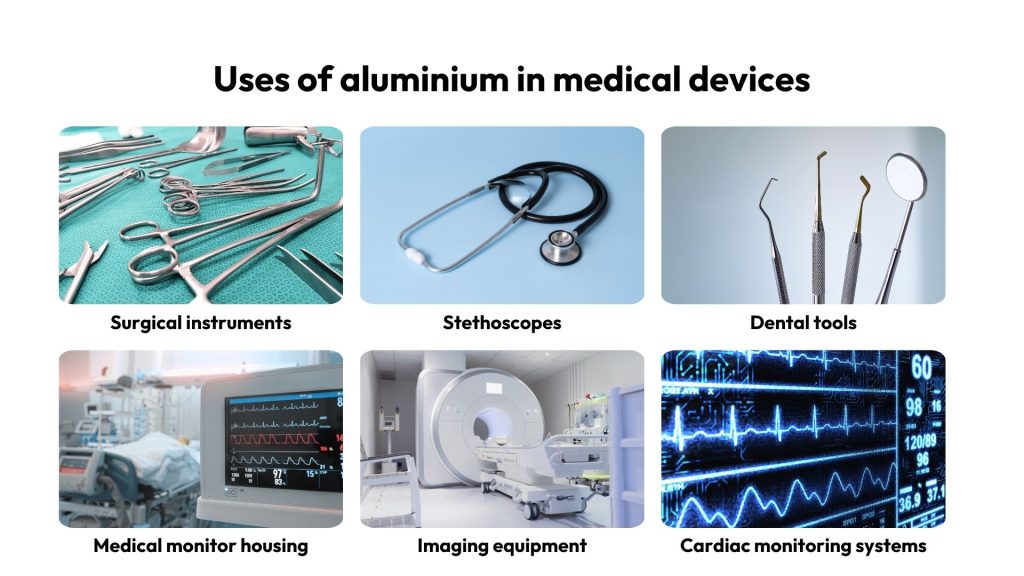
There has been a noticeable shift in consumer preferences within the pharmaceutical industry, moving away from traditional bottles towards blister packaging, which provides more convenient unit-dose options. In the healthcare sector, blister packs are widely used for both pharmaceuticals and medical devices, but their utility also extends to the culinary, industrial, and consumer goods industries. Aluminium foil has become a crucial material in pharmaceutical packaging due to its outstanding protective qualities. Its exceptional barrier properties safeguard medications from environmental elements such as moisture, light, oxygen, and contaminants that could degrade their effectiveness.
Companies like Lotus Surgicals Pvt. Ltd, Johnson & Johnson Pvt. Ltd, Universal Sutures, Orion Sutures (India) Pvt. Ltd, etc., have incorporated the use of aluminium in their devices. Talking about Lotus Surgicals, the company was the first to introduce peelable aluminium pouch for synthetic absorbable sutures. Even Johnson & Johnson (J&J) is known to use aluminium in some of its products and recycle them once they are out of service.
Use of aluminium in construction
Materials are the building blocks that define the structures of our cities and homes. Among them, aluminium stands out as a versatile and essential material in the building and construction sectors. Its distinct properties have revolutionized the way we approach design and construction. Aluminium stands out as a metal with exceptional properties, making it an ideal choice for various applications. In the building and construction industry, it has emerged as the material of choice. Designers and architects increasingly leverage aluminium to craft unique and innovative structures that offer greater strength, lightweight characteristics, durability, and low maintenance compared to iron, steel, and many other traditional construction materials.
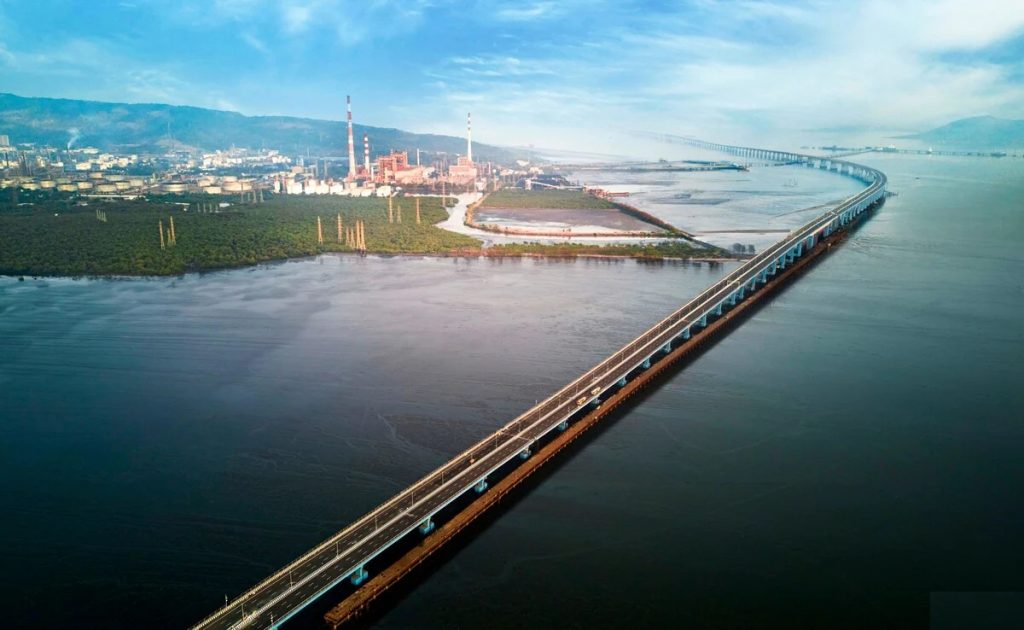
The Atal Setu Bridge in Mumbai, also referred to as the Mumbai Trans Harbour Link (MTHL), is touted as India’s longest sea bridge and the world’s 12th longest sea bridge. The Mumbai Metropolitan Region Development Authority (MMRDA) has constructed, operated and maintained the project. The bridge features aluminium as one of the construction materials, along with steel and other materials. As per Hindalco’s social media post, the company supplied around 165 MT of precision-crafted aluminium louvres in 6063 alloys for its construction. The powder-coated louvres are lightweight, durable, and elegantly designed. Beyond their aesthetic appeal, they serve as an effective sound barrier, safeguarding the habitat of flamingos and migratory birds at the Sewri mudflats. This achievement beautifully combines functionality with environmental stewardship.
India’s move towards green transition
India is leading a transformative shift in the global energy landscape. The global push for cleaner energy has substantially increased the demand for industrial metals, with aluminium emerging as a key beneficiary. According to the International Aluminium Institute, the renewable energy sector is poised to drive significant growth in aluminium demand, owing to its critical role in manufacturing solar panels and facilitating power distribution.
Rural electrification is set to play a pivotal role in driving aluminium demand across India. How – by addressing the critical gap in electricity distribution between rural and urban areas. To address this disparity, the government launched the Deen Dayal Upadhyaya Gram Jyoti Yojana (DDUGJY) in December 2014 and the Pradhan Mantri Sahaj Bijli Har Ghar Yojana (SAUBHAGYA) in October 2017. These initiatives aim to strengthen electricity distribution networks and bring power to rural households. India’s commitment to generating 50 per cent of its electricity from renewable sources by 2030 and achieving net-zero carbon emissions by 2070 represents a significant milestone in the global effort to combat climate change.
Aluminium is indispensable in clean energy technologies, especially in photovoltaic (PV) solar panels, accounting for 85 per cent of components such as frames and mounting structures. These elements are critical for securing and supporting PV panels. In wind power, lightweight aluminium alloys are used in turbine blades and tower platforms, particularly offshore farms. Their high strength-to-weight ratio and excellent corrosion resistance enhance both efficiency and durability, making them ideal for such applications.
India’s transition to green energy is a cornerstone of its sustainable development strategy. As the nation strives to meet its growing energy demands through clean and renewable sources, the aluminium industry is set to play a critical role in this transformation. With sustained government backing and strategic investments, India has the potential to establish itself as a global leader in the renewable energy market, driving progress toward a more sustainable future.
Conclusion
Aluminium’s role in national security is rapidly expanding to encompass futuristic applications, including robotic systems, underwater vehicles, and advanced sensing technologies, paving the way for more efficient and innovative defence solutions. India’s defence sector is evolving into a dynamic hub, fostering a unified R&D framework that brings together diverse industries. As public and private stakeholders increasingly collaborate, their joint efforts in advancing technologies and developing robust materials like aluminium will significantly enhance India’s military capabilities.
In an increasingly dynamic geopolitical landscape, India must intensify its efforts to become a self-sufficient producer of defence equipment and technologies. By cultivating a robust domestic defence ecosystem, the nation can position itself as a dominant player in the global defence market. Aluminium will play a pivotal role in advancing the ‘Make in India’ initiative, bolstering the country’s long-term vision of a self-reliant defence sector, securing its borders, and strengthening its global standing in defence manufacturing.